Case Study: Masana Petroleum
From Reactive to Proactive: How Petroleum Solutions Provider Masana Digitized EHS Risk Management
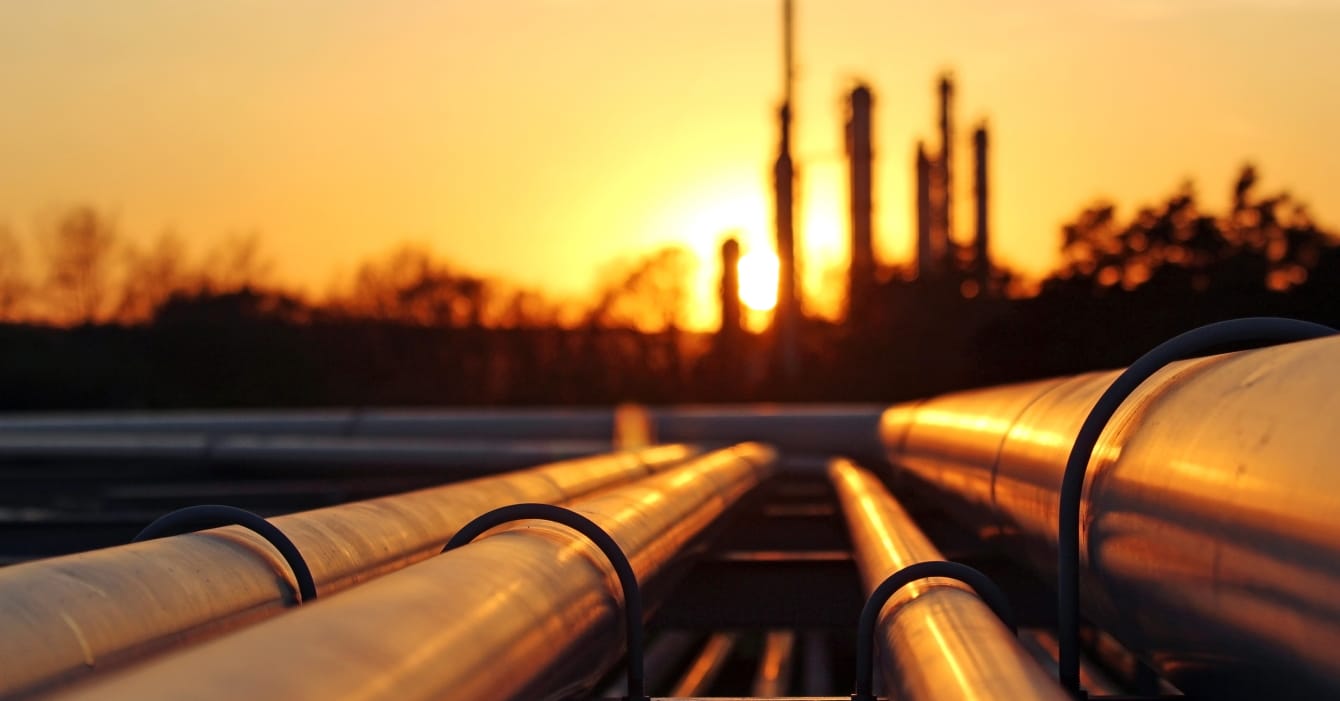
Quick Facts
Solutions being used: IsoMetrix EHS Solution
Number of depots: 11
Number of on-road filling stations: 350+
Masana provides petroleum products and solutions to various business-to-business sectors in South Africa, including the mining industry. The organization represents part of BP’s BEE initiative in South Africa, and is 51% owned by BP. All Masana’s diesel and petroleum products are sourced from BP.
Masana approached IsoMetrix to replace their manual and paper-based systems for managing its Governance, Risk and Compliance universe. The company needed a technology solution that brings their data into a centralized location, saves time creating detailed and accurate board reports and allows their HSE team to conduct trend analysis and manage risks by exception.
“We needed a system that would bring all of our data together to give us a single source of truth.”
– Mashiza Zama, HSSE Manager at Masana Petroleum Solutions
Background
When Mashiza Zama, HSSE Manager at Masana Petroleum Solutions joined the organization, he immediately put his experience with digital risk management systems to work. “When I joined Masana, there was no system in place to manage HSE requirements.”
“There were multiple, disjointed spreadsheets and it was extremely difficult to collate data and get an accurate picture of what was really going on in the business. We had no way to track HSE incidents, or actions related to the incidents,” he explains. “We needed a system that would bring all of our data together to give us a single source of truth.”
Masana experienced the same problems that many organizations face when using manual systems. “Data was constantly getting lost,” Mashiza says. “Incidents would be investigated, but the records would get lost. I could not get the historical data to determine what had happened before I joined.” Data was scattered in many spreadsheets, and it was time consuming to try collating data to build reports.
Sanelisiwe Xaba, HSSE Coordinator at Masana Petroleum Solutions, confirms this, saying, “It was a nightmare, you could not do trend analysis of any sort. Now with IsoMetrix, we are able to track trends and manage by exception.”
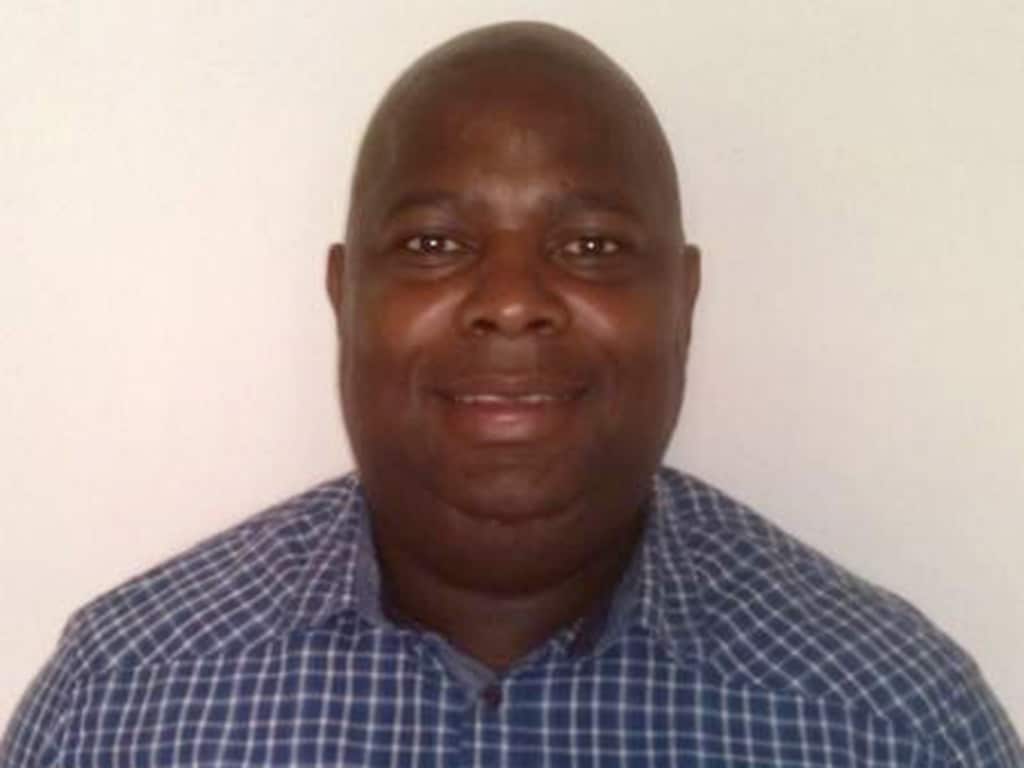
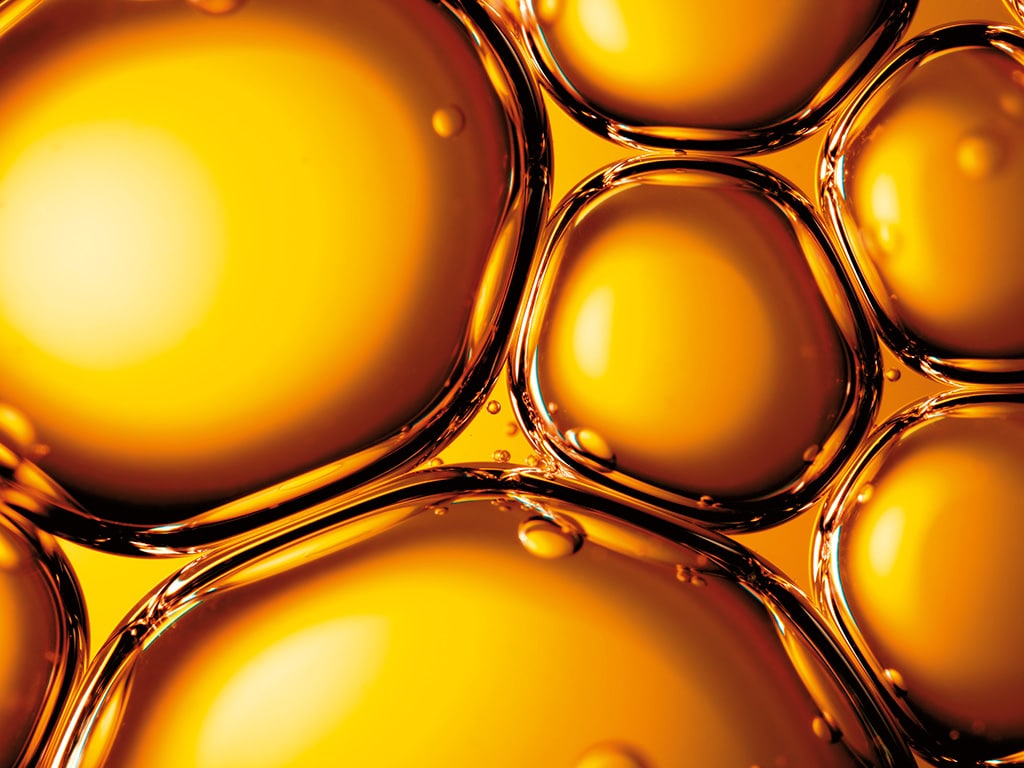
The Central Action Manager
Mashiza explains that the module in IsoMetrix that his team derive the most benefit from is the Central Action Manager. The Central Action Manager is the heart of any IsoMetrix system. Actions are assigned to users in the system ensuring the close-out of all tasks and processes. Actions manage the process by which employees are held accountable for their responsible tasks.
Actions and their progress are easily visible via the dashboards where they can be sorted by user and status.
The Central Action Manager allows Mashiza and Sanelisiwe to assign responsibility for each action and keep track of the status of each action. The system sends reminders of outstanding actions and manages escalations within the system.
Proactively Managing Risk
Mashiza explains that it is important for Masana to have a Risk Management software tool that allows him and his team to be proactive in their risk management. This is nearly impossible to accomplish with manual and spreadsheet-based systems. An important aspect of managing their risk proactively is being able to perform trend analysis. They can see if certain non-conformances and incidents occur repeatedly. It allows for deeper insight into the business.
“We needed an integrated HSE management system that links audit, risks and incidents. We needed to see everything on a single platform.” When there is a non-conformance, the HSE department at Masana can easily check if the non-conformance has already been identified as a risk or caused an incident in the past. This helps them to implement preventative measures.
“We can take more control of our risk management by being proactive. We would not be able to do this without having all of our data in one place, and that place is in our IsoMetrix system” he says.
“IsoMetrix was always able to help us iron out our requirements. The subject matter expert helped us to configure the system to match our requirements exactly and help us to get the most out of the software.”
– Mashiza Zama, HSSE Manager at Masana Petroleum Solutions
Working with the IsoMetrix Team
Mashiza and Sanelisiwe both emphasize how much they enjoy working with the IsoMetrix team. During the project implementation, Masana found the IsoMetrix team to be knowledgeable and helpful.
“IsoMetrix was always able to help us iron out our requirements. The subject matter expert helped us to configure the system to match our requirements exactly and help us to get the most out of the software.”
Since going live with the system, any issues that naturally arise have been dealt with, swiftly and enthusiastically.
“We find our account manager to be engaging, and attentive,” says Sanelisiwe. “The team continues to work closely with us to help us get the most out of the system, and anticipate our needs. The support team is also wonderful, we work closely with them, and whenever we encounter an issue, the team is on hand to resolve it as quickly as they can.”
Summary
Masana now has a fully integrated Risk and Compliance Management system that can be used by SHEQ Managers, Compliance Officers, Internal Audit, Risk Managers and Risk Practitioners, and Forensics.
Reports and information are accessed online, and can be extracted from the system and reported to the various committees and the Board. Masana can also now track and report on all risks regularly and accurately.
Masana now has a fully integrated Risk and Compliance Management system that can be used by SHEQ Managers, Compliance Officers, Internal Audit, Risk Managers and Risk Practitioners.